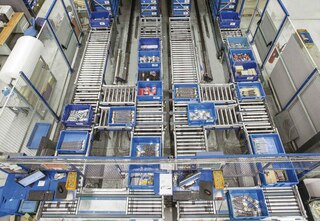
Sistema Kanban: o que é e como funciona na logística?
O sistema Kanban é responsável por organizar o fornecimento e a produção de mercadorias em processos da produção que operam sob a metodologia just-in-time (JIT), que é quando apenas a matéria-prima necessária está disponível no momento certo. O objetivo final é ajustar a capacidade de produção com a procura para evitar excessos de stock e esperas desnecessárias entre os processos.
Foi na empresa japonesa Toyota que o sistema Kanban foi idealizado na década de 50, como parte da metodologia de Lean manufacturing, (minimizar desperdícios para aumentar a produtividade). Foi o engenheiro industrial Taiichi Ohno quem projetou este modelo de produção, que se revelou como a solução para enfrentar a profunda depressão em que se afundou a indústria japonesa após a Segunda Guerra Mundial.
O que é o sistema Kanban? Definição e origem
O método Kanban estabelece um protocolo para reposição de stock. É mu sistema de comunicação para ordens de produção e reposição de materiais. É utilizado em modelos de produção que respondem diretamente à procura (sistema pull, o produto não começa a ser fabricado até que a fábrica recebe o pedido do cliente).
Taiichi Ohno concebeu o sistema Kanban inspirado nas regras de reposição dos supermercados americanos. Neles, os clientes retiram os produtos das estantes. Cada produto é etiquetado e, ao passar pela caixa, todas as referências vendidas são registadas e é emitido um pedido de reposição para o armazém, que identifica a mercadoria com o mesmo sistema. Depois que os artigos são reabastecidos no supermercado, o armazém, por sua vez, envia outro pedido de reposição para os seus fornecedores ou fabricantes e assim por diante em toda a cadeia de abastecimento. Para determinar quando começar os pedidos de reabastecimento, o método de ponto de pedido é usado.
Como funciona? Cartões e quadros Kanban
A tradução literal de Kanban em japonês é “cartões coloridos”. Isso porque, originalmente, eram utilizados cartões para solicitar as peças necessárias no processo anterior. Uma vez que o pedido de reposição fosse concluído, o cartão Kanban voltaria ao seu armário original.
Esses cartões recolhiam as informações que identificavam cada lote de material: SKU, código, tamanho do lote, destino da mercadoria, cliente que solicitou, etc. Os cartões eram pendurados em cada um dos contentores ou prateleiras onde estava o produto.
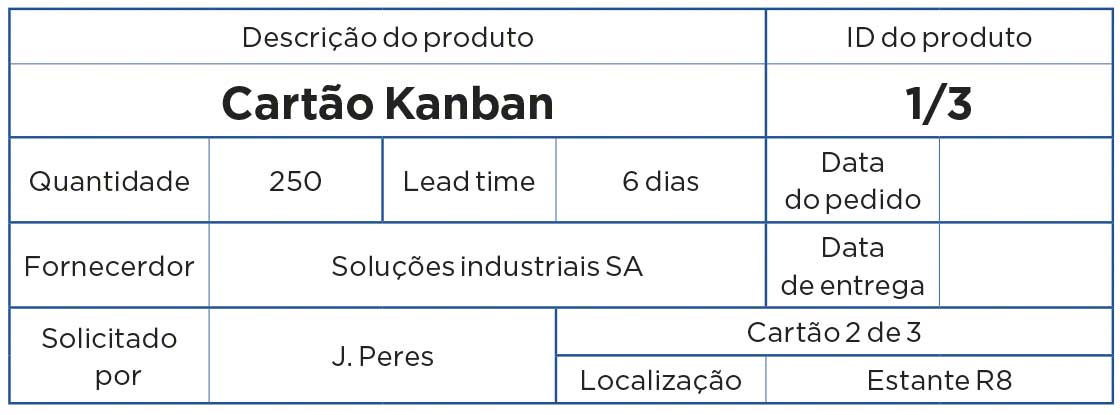
Exemplo de cartão Kanban
Atualmente, o sistema Kanban foi substituído por aplicações informáticas que acionam o processo de reposição. O sistema de trabalho também pode ser representado por quadros Kanban, que consistem em várias colunas para colocar os cartões ou etiquetas virtuais. Dessa forma, cada coluna indica o status de cada tarefa e quem é o responsável por executá-la.
Embora o método Kanban tenha surgido originalmente num contexto industrial, atualmente ele também é aplicado na gestão de todos os tipos de projetos, como, por exemplo, aqueles relacionados ao desenvolvimento de software.
Tipos de cartões Kanban
Existem dois tipos principais de cartões Kanban:
- Kanban de transporte: marca a quantidade de produto que deve ser reabastecido para cumprir o próximo processo na cadeia. Se tomarmos o exemplo do supermercado, o cartão Kanban de transporte seria usado para indicar que um tipo de produto foi vendido e deve ser transportado do armazém para a prateleira da loja.
- Kanban de produção: utilizado para solicitar a fabricação de um produto. Com o mesmo exemplo, este tipo de cartão Kanban seria emitido pelo armazém quando ficasse sem stock (porque já foi enviado para a loja).
No diagrama a seguir, vemos de forma esquemática a operação em cadeia dos cartões Kanban de produção e transporte numa linha de produção simplificada:
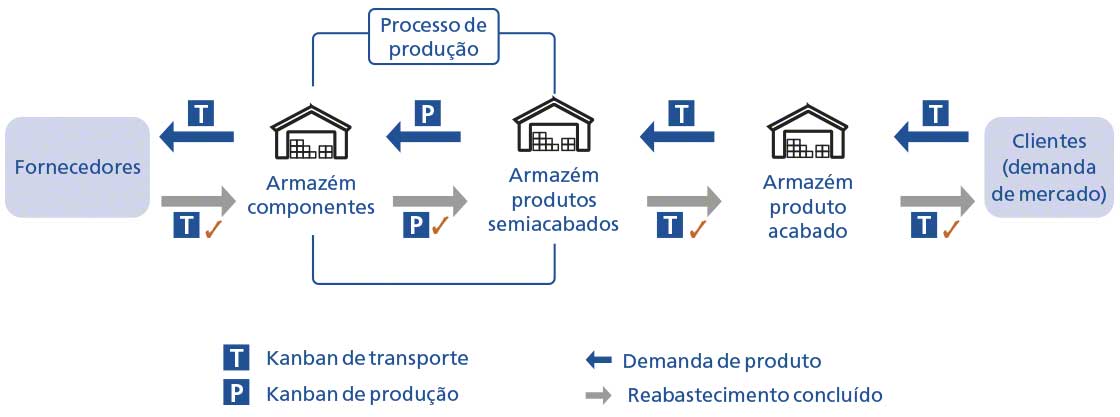
Operação simplificada do sistema Kanban com cartões de transporte e produção
Vantagens de usar o sistema Kanban em logística e produção
O método Kanban é o aliado perfeito do sistema just-in-time porque:
- Permite visualizar o desenvolvimento do trabalho e assim identificar com facilidade cada fase do ciclo de produção ou reposição.
- Com o sistema Kanban é fácil definir o limite do trabalho em curso, também chamado de WIP (work in progress) para evitar a formação de gargalos.
- É possível medir o lead time entre os processos, ou seja, o tempo que leva para concluir cada fase.
- Ao interligar as diferentes etapas, funciona como um sistema de controlo da produção e dos materiais disponíveis nas diferentes instalações de armazenagem.
- Evita cair em situações de superprodução ou excesso de stock, o que permite uma poupança de espaço de armazenagem.
Desvantagens de usar Kanban
Algumas de suas restrições fazem com que nem sempre seja o método mais adequado:
- O sistema Kanban fornece resultados ideais quando o fluxo de produção é distribuído uniformemente ao longo do ano e é organizado em séries curtas com volumes semelhantes. Por outro lado, se o negócio está sujeito a uma alta volatilidade de procura que requer ajustes abruptos na produção, o método Kanban sofre ineficiências que desestimulam o seu uso.
- Pode agravar os atrasos na cadeia de produção se algum dos elos falhar (um cartão é perdido ou um pedido é emitido incorretamente, por exemplo).
- O sistema Kanban não é o mais flexível para lidar com grandes mudanças nas técnicas de fabricação de produtos.
- Não funciona corretamente se os fornecedores não aplicam as mesmas regras Kanban para o reabastecimento.
Quando usar Kanban no armazém? O papel do SGA
Atualmente, a aplicação do sistema Kanban no armazém deixou os cartões de papel para trás: agora é aplicado nas organizações por meio de um sistema de gestão do armazém (como Easy WMS) em combinação com sistemas de identificação automática, como códigos de barras ou RFID. Cada registo no WMS funciona como um cartão Kanban, já que, ao ler os dados com um scanner, o sistema retorna todas as informações vinculadas àquele SKU.
Em logística, o método Kanban é usado para organizar a reposição de stock em diferentes níveis:
Kanban num único armazém
Se os locais dedicados ao picking e armazenagem forem divididos, o sistema Kanban é especialmente útil para reabastecer o stock das estantes picking.
Uma vez esgotadas as referências nesses locais de picking, o WMS emite um aviso automático de reabastecimento que funciona como um cartão Kanban, embora também possa ser acionado manualmente por qualquer operador ao detetar a falta de material.
Desta forma, a mudança de localização da mercadoria será programada de acordo com a prioridade, embora normalmente seja reservada para os momentos de menos exigência da instalação (por exemplo, é o caso do wave picking ou picking por ondas).
Se no momento da transferência da mercadoria do armazém para o picking observar que as referências também terminaram na área de armazenagem, o WMS pode enviar uma notificação direta ao departamento de compras para que este tenha em consideração nas solicitações de pedidos aos fornecedores.
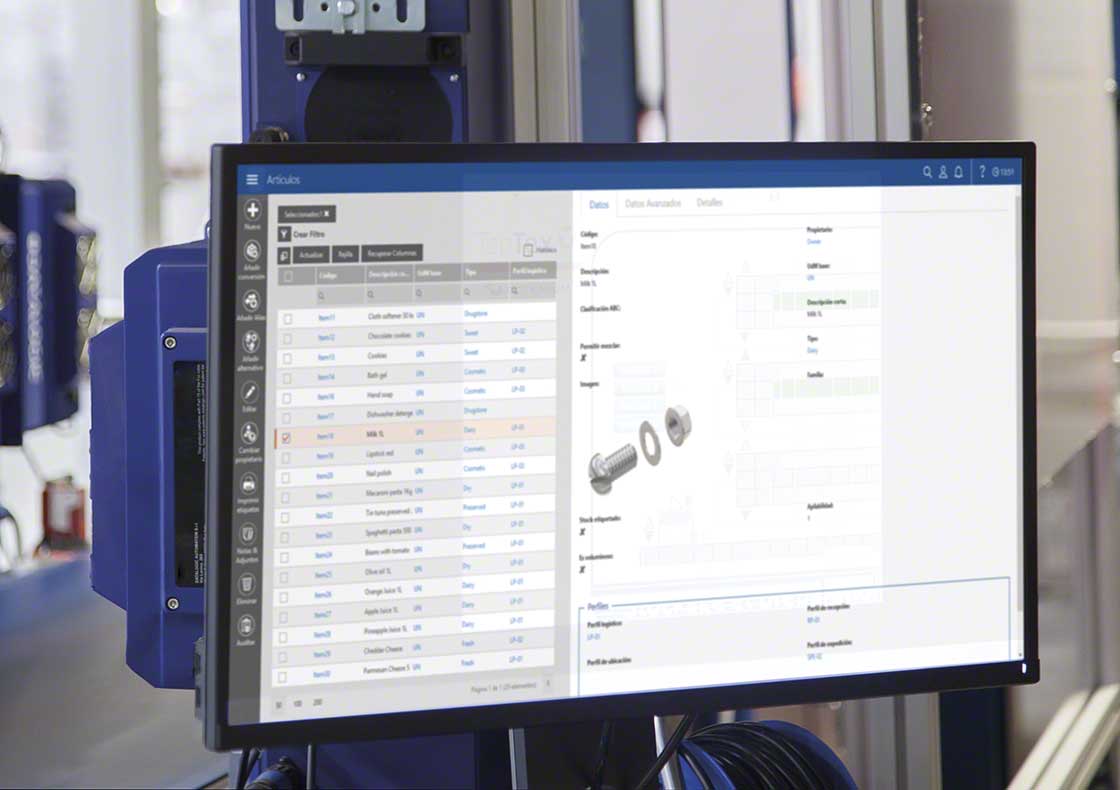
O reabastecimento do stock de componentes pode ser programado seguindo o sistema Kanban
Kanban numa rede de armazéns logísticos
O sistema Kanban também pode ser aplicado em empresas que trabalham com stock distribuído em diversos armazéns. Eles podem atender a mesma linha de produção (como na logística de produção) ou fazer parte da mesma rede logística (como nas redes logísticas do retalho).
Vamos ver em detalhe como o Kanban funciona em cada caso e quais as funções o SGA executa:
- Kanban nos armazéns de produção: a principal peculiaridade das instalações que abastecem as fábricas é que manipulam stocks classificados em matérias-primas, produtos semiacabados e produtos acabados. Para que não ocorra nenhuma rutura de stock no processo produtivo, é fundamental manter o controlo de stock informatizado. Nesse sentido, o WMS para produção opera seguindo o método Kanban, pois, ao se deparar com um novo pedido, o SGA lança ordens de serviço para a fábrica e monitora o stock de segurança disponível de cada referência.
- Kanban nas cadeias de abastecimento de retalho: neste caso, a rede logística é composta por armazéns (centrais e regionais) e lojas físicas. Seguindo o método Kanban, a procura pelos produtos é registada no ponto de venda e, a partir daí, os pedidos de reposição são gerados para os armazéns. Aqui, o SGA funciona como um catalisador para a reposição entre os centros, uma vez que contém os dados globais de stock. Além disso, se tomarmos como exemplo o Easy WMS da Mecalux, com o módulo Store Fulfillment é possível organizar e ordenar movimentos de stock entre centros sem intermediários: isso permite aproveitar ao máximo a capacidade logística da empresa.
Gestão de stock com o sistema Kanban
Aplicar o sistema Kanban tradicional com inventários extensos distribuídos entre diferentes centros e lidar com um volume muito alto de SKUs é ineficiente devido à complexidade crescente. No entanto, é possível planificar a reposição de stock e aproveitar as vantagens do método Kanban com a ajuda de um SGA.
O Easy WMS possui funcionalidades avançadas para a gestão integrada de stock e permite operar com diferentes regras de reposição. Se deseja saber mais sobre o funcionamento do nosso SGA, entre em contato connosco e um dos nossos especialistas explicará detalhadamente como pode contribuir para a gestão otimizada do seu armazém.