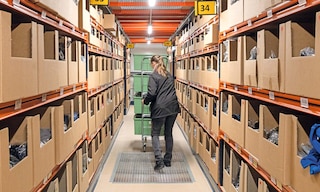
45 estratégias para melhorar o picking do armazém
A preparação de pedidos costuma ser uma das operações que mais dores de cabeça causa num armazém devido à sua complexidade, custos e risco de erros, entre muitas outras razões. Neste artigo detalhamos 45 estratégias que, aplicadas corretamente, podem ajudar a reduzir os custos que a fase de picking representa para a empresa, aumentando a agilidade e, sobretudo, limitando as falhas nessa etapa logística.
1. Projetar um layout de armazém eficiente
O projeto do layout do armazém deve garantir que as áreas de picking estejam bem delimitadas e organizadas de acordo com a ordem em que o pedido é preparado: do recebimento ao armazenamento, passando pelas áreas de reabastecimento, de preparação de pedidos ou de embalagem. É importante coordenar a operação para que não ocorram movimentos desnecessários.
2. Separar a área de picking da área de devolução de produtos
É um erro comum situar os postos de devolução de produtos perto das áreas de preparação de pedidos. Separar ambas as áreas, previne perdas de stock e evita o descontrole na gestão do stock.
3. Implementar um SGA para digitalizar a gestão do stock
A implantação de um software de gestão de armazém garante a rastreabilidade total de produto e um controle exaustivo da preparação de pedidos. O programa organiza as diferentes estratégias de picking, além de indicar ao operador o procedimento passo a passo a ser seguido nessa fase.
4. Localizar a mercadoria de forma eficiente
O chefe de armazém deve determinar um conjunto de critérios e regras de localização da mercadoria baseando-se na procura real de pedidos no armazém (rotatividade, tipo de produto, etc.). A implementação de um software de gestão de armazém minimiza o risco de falhas nessa operação e otimiza o slotting, ou seja, a gestão de localizações no armazém.
5. Escolher sistemas de armazenagem que se adaptem ao armazém
O planejamento logístico deve incluir os sistemas de armazenagem que melhor se adaptem às características do armazém, aos tipos de produto que são armazenados ou aos fluxos de mercadoria e de stock que existem na instalação.
6. Utilizar estantes dinâmicas para separar operações
As estantes para picking dinâmico são ideais porque permitem aumentar o número de linhas de picking e reduzir as deslocações dos operadores. Esses sistemas de armazenagem multiplicam a eficiência do picking de unidades soltas.
7. Picking em estantes de paletes
O picking sobre paletes é uma solução adequada quando cada palete contém apenas uma referência. Da mesma forma, para fazer a preparação de pedidos numa estante de paletes é recomendável que as referências de maior consumo estejam localizadas nos níveis mais baixos.
8. Traçar rotas de picking para maximizar a agilidade e eficácia
Os percursos dos operadores representam uma grande parte do custo da preparação de pedidos. Um software de armazém (como o Easy WMS da Mecalux) permite otimizar os percursos dos operadores considerando o método de picking e o slotting predeterminado pelo responsável logístico.
9. Dedicar mais espaço ao picking
Os sistemas de armazenagem compactos, como as estantes drive-in, Movirack ou Pallet Shuttle, reduzem o espaço destinado ao armazenamento para assim dedicar a maior parte do armazém à preparação de pedidos.
10. Identificar os pontos de estrangulamento
É essencial que o responsável logístico ouça os funcionários e detete pontos de estrangulamento, assim como possíveis melhorias nos métodos de picking. Por outro lado, um software como o módulo do Easy WMS Labor Management System pode ajudar a detetar ineficiências e a equilibrar cargas de trabalho entre os diferentes operadores.
11. Integrar o SGA com o ERP
As operações dirigidas pelo SGA devem estar alinhadas com as estratégias da empresa. É necessário sincronizar o SGA com o sistema ERP para comunicar automaticamente as informações sobre o pedido referências ou condições de entrega, garantindo a, comunicação bidirecional entre o departamento de logística e as outras divisões da empresa.
12. Monitorar o stock em tempo real
O controle de stock é uma das operações essenciais para a eficiência na preparação de pedidos. Digitalizar o stock com um SGA é a melhor forma de monitorar em tempo real o stock do armazém.
13. Reabastecer as localizações a tempo
Não existe nada mais ineficiente para o picking de uma empresa do que chegar a uma localização e não ter um dos produtos que compõem o pedido. Para otimizar as deslocações dos operadores é necessário garantir o tempo todo uns níveis mínimos de stock (stock de segurança), assegurando um reabastecimento constante de produtos nas localizações de armazenamento.
14. Digitalizar e automatizar a documentação
A preparação manual de pedidos exige gerir documentação básica como notas de entrega, picking lists ou rotas. Fazê-lo em papel aumenta a probabilidade de cometer erros. Um SGA automatiza, por exemplo, a gestão de picking lists para que o operador tenha apenas que seguir as indicações dadas pelo software.
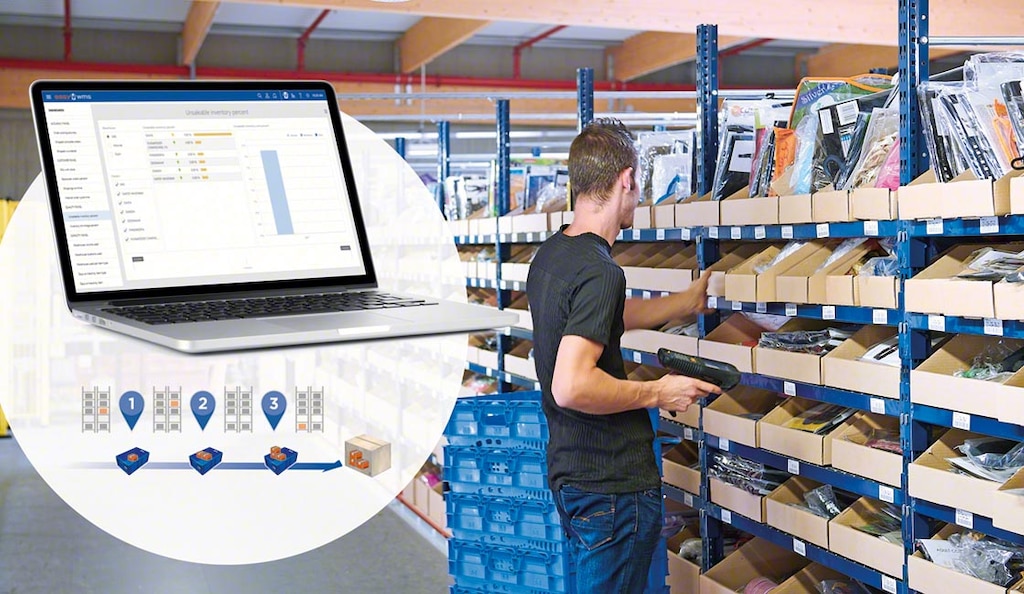
15. Definir os KPI mais adequados
O responsável logístico deve selecionar os KPIs logísticos relacionados à preparação de pedidos que melhor se adaptem ao tipo de negócio, às características do produto ou às diferentes estratégias de picking realizadas no armazém.
16. Automatizar a medição de resultados
Para conseguir a máxima produtividade na preparação de pedidos é essencial confiar numa ferramenta que automatize a análise de dados. Um programa como o módulo de Easy WMS Supply Chain Analytics oferece ao responsável logístico uma visibilidade constante do desempenho real do armazém.
17. Calcular o ciclo de ordem interna
Esse indicador de desempenho determina o tempo que leva preparar um pedido desde que a ordem entra no sistema (via ERP ou SGA) até ser completada. Esse cálculo ajuda a controlar o stock do armazém, a eficiência na preparação de pedidos e o serviço logístico ao cliente final.
18. Prever as mudanças na procura
Os critérios e regras preestabelecidos para a localização de produtos devem ser verificados constantemente visando detetar as mudanças nas tendências do mercado, a sazonalidade de certos produtos ou os picos de procura. A previsão de possíveis cenários, graças às ferramentas de análise preditiva, permite tomar decisões baseadas no desempenho real do armazém.
19. Automatizar o fluxo da mercadoria
Substituir os equipamentos de movimentação manuais por sistemas de transporte automatizados como os transportadores para caixas permite acelerar o movimento da mercadoria rumo às estações de picking.
20. Implantar sistemas de assistência ao picking
Uma estratégia fundamental para maximizar a eficiência do picking é implantar métodos de preparação de pedidos semiautomáticos. Sistemas como o pick-to-light ou o picking por voz permitem que o software de gestão de armazém guie o operador, indicando-lhe passo a passo as tarefas que deve realizar.
21. Explorar soluções de robótica
Os robôs pick and place complementam o picking reorientando os trabalhos dos operadores para tarefas de valor agregado como a preparação de pedidos personalizada. Por outro lado, os cobots (robôs colaborativos) representam uma solução que facilita o trabalho dos operadores, interagindo com eles e encarregando-se das tarefas mais físicas e pesadas da preparação de pedidos.
22. Automatizar o picking com um sistema 'goods-to-person'
O goods-to-person é uma estratégia de preparação de pedidos onde a mercadoria chega ao operador através de sistemas de transporte automatizados, tais como transportadores para paletes ou caixas. O SGA encarrega-se de coordenar toda a operação para garantir um picking eficiente.
23. Melhorar os recebimentos
Um processo de recebimento de mercadoria organizado e eficaz agiliza a preparação de pedidos. Na área de recebimento de mercadoria, é habitual equipar os operadores com terminais de radiofrequência ligados ao software de gestão de armazém para aumentar o controle dos recebimentos e a velocidade dos fluxos de produto para as diferentes áreas de armazenamento ou picking.
24. Estabelecer estratégias de picking adequadas
Determinar antecipadamente as estratégias de picking em função dos fluxos de mercadoria e do tipo de produto reforça a eficiência da instalação. Alguns dos principais métodos de preparação de pedidos são, por exemplo, o picking por ondas, o batch picking ou o picking por áreas.
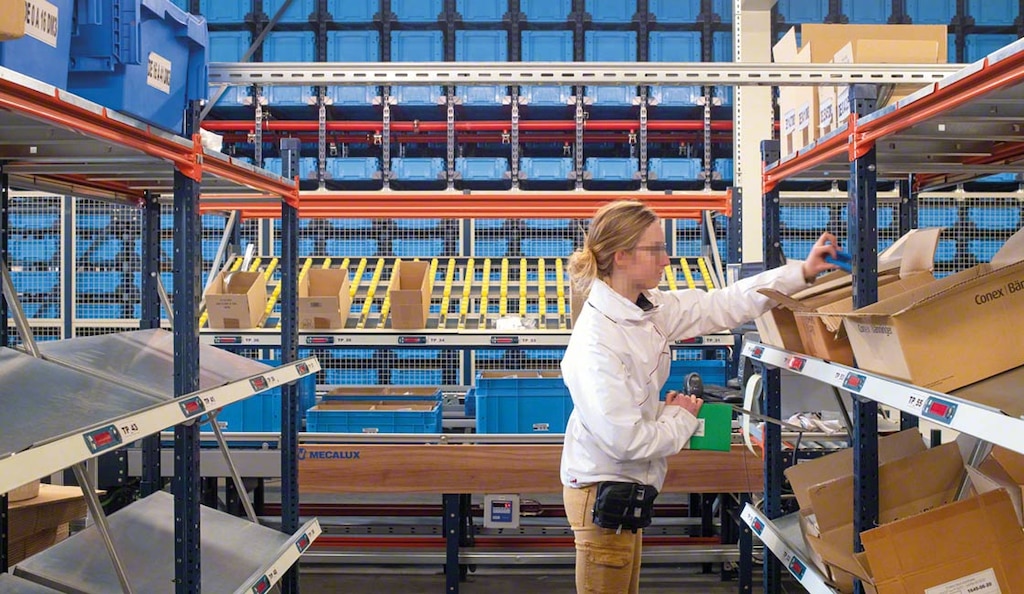
25. Experimentar o 'pick-to-box'
Um método manual para a preparação de pedidos que pode ser altamente rentável é o pick-to-box ou pick-to-tote, ou seja, os carrinhos levam a caixa pronta para ser enviada (shipping box). Dessa forma, consegue-se unificar numa única fase três etapas diferentes do picking: recolha, consolidação e embalagem dos produtos.
26. Avaliar os benefícios do ‘cross-docking’
O cross-docking é uma técnica de preparação de pedidos que consiste em distribuir a mercadoria diretamente ao cliente final sem passar por um período de armazenamento prévio. Esse método exige incluir espaços no armazém ou sistemas de armazenagem específicos que atuem como buffer temporário dos produtos recebidos.
27. Etiquetar corretamente os produtos do armazém
Uma etiquetagem inadequada pode arruinar a melhor das estratégias de picking. Por essa razão, é crucial que o responsável logístico valide o processo de etiquetagem para garantir o bom funcionamento do sistema.
28. Aplicar uma filosofia ‘lean’
O lean logistics é uma filosofia de organização das operações realizadas no armazém que procura a máxima eficiência em todas as operações, eliminando aquelas que não proporcionam valor agregado. É preciso analisar os processos da preparação de pedidos e identificar as fases desnecessárias para atingir a máxima produtividade.
29. Eliminar movimentos desnecessários
Para melhorar o picking é preciso otimizar todos os movimentos e picks realizados por um operador no armazém. Qualquer percurso supérfluo pode aumentar o custo logístico do produto.
30. Estruturar as listas de picking
No momento de elaborar as listas de picking é importante considerar a ordem em que devem ser colocados os produtos que compõem a lista para que caibam na caixa de envio. Um SGA pode sequenciar os movimentos para que se recolha em primeiro lugar as referências de maior tamanho.
31. Integrar medições de produto no SGA
As medidas e o peso da mercadoria podem ser integrados no sistema de gestão de armazém para aumentar a precisão na preparação de pedidos. Por exemplo, se faltar uma unidade de um produto, o próprio software sinalizará que o pedido ainda está incompleto.
32. Evitar colocar inúmeras referências de diferentes pedidos num mesmo carro
Localizar diferentes produtos de diferentes pedidos num mesmo carro aumenta o risco de erro, especialmente quando o operador não estiver sendo auxiliado por algum dispositivo. Qualquer falha durante essa operação pode representar um maior tempo na preparação de pedidos e um aumento nos custos.
33. Realizar o 'kitting' antes do picking
Para obter a máxima eficiência na preparação de pedidos, a montagem de kits deve ser realizada antes do processo de picking. Se não for possível calcular o número exato de kits necessário, é recomendável preparar alguns antecipadamente.
34. Minimizar as devoluções de produtos
Um software de gestão de armazém é a ferramenta ideal para eliminar o risco de erro e minimizar as devoluções de produto decorrentes de um picking incorreto.
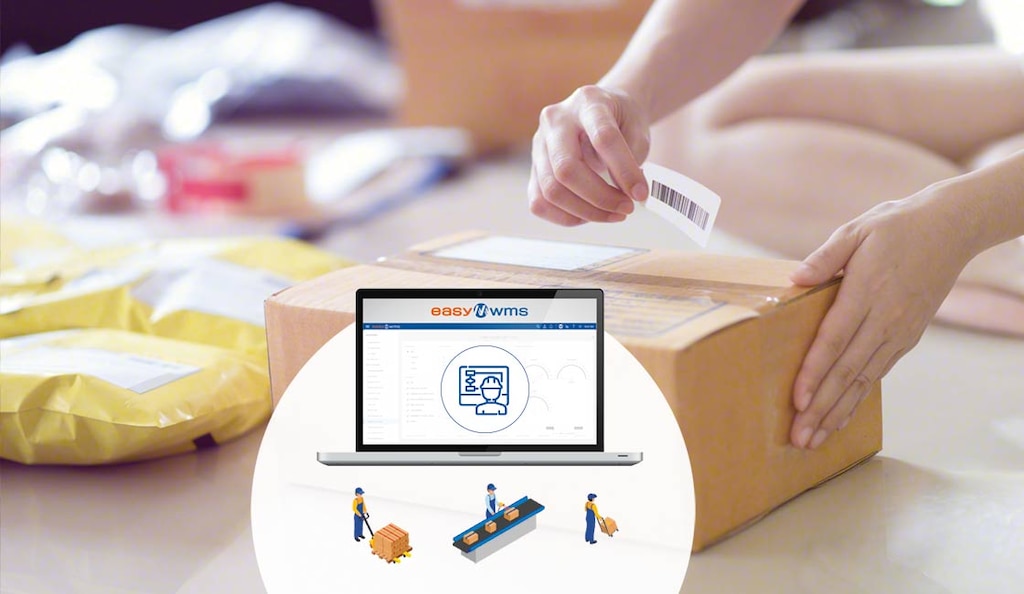
35. Garantir que todos os funcionários tenham o equipamento necessário
Os operadores devem ter todo o material necessário para executar as tarefas no menor tempo possível: terminais de radiofrequência, carros, porta paletes, empilhadores elevadores, etc.
36. Criar estações de trabalho ergonómicas
As estações de preparação de pedidos exigem desenhos ergonómicos para proporcionar conforto ao operador. Esses postos de trabalho também devem estar equipados com todos os elementos de trabalho para evitar deslocações desnecessárias.
37. Garantir a segurança da instalação
Qualquer processo é mais ágil e rápido se houver um ambiente industrial seguro para a instalação, mercadoria e operadores onde a ordem e a limpeza da instalação sejam uma prioridade.
38. Sinalizar corretamente o armazém
É necessário ter um armazém eficiente e, sobretudo, seguro, por isso é preciso sinalizar corretamente as diferentes partes da instalação. Nas operações de picking coincidem operadores, mercadoria e equipamentos de movimentação, manuais ou automáticos, e uma sinalização inadequada poderia aumentar o risco de incidentes.
39. Iluminar convenientemente o armazém
A correta iluminação dos armazéns ajuda os preparadores de pedidos a identificar as localizações de armazenamento, além de reforçar a segurança dentro da instalação. A iluminação é um fator especialmente relevante em instalações logísticas onde operam equipamentos de movimentação manuais.
40. Formar os operadores
Para que a preparação de pedidos seja eficiente, é primordial formar os operadores no uso dos diferentes sistemas de armazenagem, equipamentos de movimentação e, inclusive, produtos. Os pickers devem conhecer em detalhes a distribuição da instalação, as mudanças no slotting dos produtos e a sinalização do armazém.
41. Informar internamente sobre a estratégia
É recomendável que o pessoal entenda a estratégia de gestão do armazém, justificando o porquê da execução de cada operação realizada na instalação.
42. Implantar técnicas de gamificação
Como em qualquer ambiente de trabalho, fortalecer a motivação e a competitividade é um dos fundamentos para conseguir o máximo desempenho num armazém. É cada vez mais comum utilizar técnicas de gamificação -competições, picker do mês, etc.,- para aumentar o compromisso dos funcionários.
43. Avaliar o apoio num 3PL
Diante de aumentos inesperados na procura, as empresas podem recorrer a um fornecedor de logística terceirizado (3PL) para apoiá-las nas operações de armazenamento e picking.
44. Diversificar as estratégias à medida que o negócio cresce
As novas tendências de mercado exigem armazéns flexíveis, aptos para se adaptar a qualquer mudança na procura ou interrupção na cadeia de abastecimento. É preciso poder trabalhar com uma logística elástica e formar os operadores para que estejam preparados diante de qualquer imprevisto.
45. Verificar periodicamente os processos logísticos
Os armazéns exigem uma planificação logística flexível, capaz de verificar constantemente o fluxo de movimentos na preparação de pedidos para se adaptar às mudanças no tipo de SKU, nos fluxos da cadeia de abastecimento ou na consolidação de pedidos para os clientes.
Um picking altamente eficiente para os novos tempos
As tendências de consumo atuais exigem multiplicar a eficiência de todas as operações logísticas, em particular as mais custosas, tal como a preparação de pedidos. É preciso considerar que os padrões logísticos do comércio eletrónico (espaço de tempo curto para a entrega e devolução gratuita de produtos, entre outros) fazem com que os armazéns tenham que melhorar o desempenho das suas estações de picking. A implementação de um software de gestão de armazém garante o aumento da produtividade do armazém.
A Mecalux está especializada em soluções de armazenagem e intralogística que promovem a eficiência e a produtividade do armazém. Se deseja otimizar a sua logística e os seus processos de picking, não hesite em entrar em contato connosco, um técnico especializado terá prazer em lhe oferecer a melhor solução para as suas necessidades.